Highlight of energy efficiency in Haiphong
Thứ tư, 14/09/2011 - 11:48
During the dry season, to help power sector reduce power consumption during peak hours, some oil-powered generators have been used, especially during peak hours, to reduce the time of using the national grid. Specifically, 65% of devices have been separated from the grid and powered by generators.
As a member of the Hanoi Beer - Alcohol - Beverage Corporation, San Miguel Yamamura Haiphong Glass Co., Ltd specializes in manufacturing glass bottle products for wine, beer and soft drink production.
The types of energy mainly used in the company are DO oil, FO oil and electricity. However, previously, like many other small and medium businesses, due to the neglect of applying energy saving measures in production, many devices of the company did not operate at full capacity or were not installed properly to use energy efficiently.
Specifically, the lighting systems used lamps with poor lighting performance; workshops did not take advantage of natural light. At that time, to meet the demand of the market, each day, the total power capacity needed to serve the production of the company was up to 34,000 kWh. To ensure production needs while saving production costs, the company has implemented a series of energy saving measures.
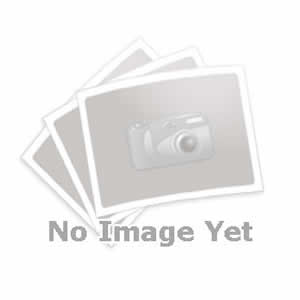
Realizing that energy efficiency shall reduce production costs, increase competitiveness for the businesses, ensure stable incomes for officials and employees, the first thing the company implements is offer a series of solutions to raise the employees’ awareness of saving power. Some solutions have been implemented such as enhancing the awareness of energy saving in the use of air conditioners by setting the temperature at a reasonable level, using electric lights appropriately. The slogan "Turn off the power when going out of office" has been popularized to each employee of the company.
Besides solutions to raise the awareness of saving electricity are technical solutions to reduce power consumption. In addition to common energy saving measures like turning off lights, air conditioners or electrical equipment when leaving the office, the company has cut all of production equipment which can be turned off, especially during peak hours. Some previously used devices such as lights, refrigeration equipment which had high design capacity and run at the minimum level have now been replaced by devices that have smaller capacity but still ensure production while saving energy.
The old incandescent bulb system has been replaced with energy saving and high efficiency compact lamps. Also, the panels have been expanded to take advantage of natural light to illuminate workshops. In addition, large pumps have been replaced with smaller pumps to ensure adequate supply of water for production without causing waste. With a series of measures mentioned above, every day, the company has saved nearly 3,000 kilowatt hours.
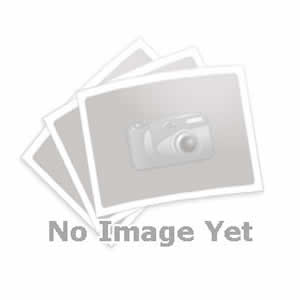
During the dry season, to help power sector reduce power consumption during peak hours, some oil-powered generators have been used, especially during peak hours, to reduce the time of using the national grid. Specifically, 65% of devices have been separated from the grid and powered by generators.
During the time of changing products, some unnecessary auxiliary systems such as oil drying system, pumping system… have been totally shut down instead of being set at standby mode. Through these solutions, the company has decreased 19,000 out of 34,000 kWh consumed per day.
With all of those solutions, the company has gained great efficiency and become one of the typical small and medium businesses in Haiphong in the application of energy saving measures in production.
The types of energy mainly used in the company are DO oil, FO oil and electricity. However, previously, like many other small and medium businesses, due to the neglect of applying energy saving measures in production, many devices of the company did not operate at full capacity or were not installed properly to use energy efficiently.
Specifically, the lighting systems used lamps with poor lighting performance; workshops did not take advantage of natural light. At that time, to meet the demand of the market, each day, the total power capacity needed to serve the production of the company was up to 34,000 kWh. To ensure production needs while saving production costs, the company has implemented a series of energy saving measures.
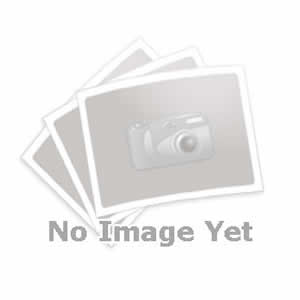
Realizing that energy efficiency shall reduce production costs, increase competitiveness for the businesses, ensure stable incomes for officials and employees, the first thing the company implements is offer a series of solutions to raise the employees’ awareness of saving power. Some solutions have been implemented such as enhancing the awareness of energy saving in the use of air conditioners by setting the temperature at a reasonable level, using electric lights appropriately. The slogan "Turn off the power when going out of office" has been popularized to each employee of the company.
Besides solutions to raise the awareness of saving electricity are technical solutions to reduce power consumption. In addition to common energy saving measures like turning off lights, air conditioners or electrical equipment when leaving the office, the company has cut all of production equipment which can be turned off, especially during peak hours. Some previously used devices such as lights, refrigeration equipment which had high design capacity and run at the minimum level have now been replaced by devices that have smaller capacity but still ensure production while saving energy.
The old incandescent bulb system has been replaced with energy saving and high efficiency compact lamps. Also, the panels have been expanded to take advantage of natural light to illuminate workshops. In addition, large pumps have been replaced with smaller pumps to ensure adequate supply of water for production without causing waste. With a series of measures mentioned above, every day, the company has saved nearly 3,000 kilowatt hours.
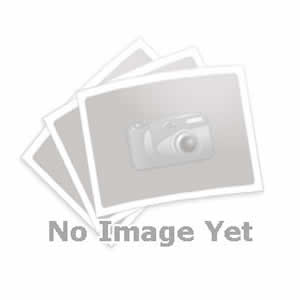
During the dry season, to help power sector reduce power consumption during peak hours, some oil-powered generators have been used, especially during peak hours, to reduce the time of using the national grid. Specifically, 65% of devices have been separated from the grid and powered by generators.
During the time of changing products, some unnecessary auxiliary systems such as oil drying system, pumping system… have been totally shut down instead of being set at standby mode. Through these solutions, the company has decreased 19,000 out of 34,000 kWh consumed per day.
With all of those solutions, the company has gained great efficiency and become one of the typical small and medium businesses in Haiphong in the application of energy saving measures in production.
By Minh Duc