A new Quality Meat Scotland (QMS) report has highlighted the potential for Scottish pig farmers to further reduce their on-farm use of energy and the price they pay for it.
Farm feedmill and feed mixing costs can account for up to 38% of annual farm electricity consumption on Scottish pig units, according to the report published today (Thursday 4 December 2014).
The publication was prepared for QMS by Livestock Management Systems Ltd and Farm Energy Consulting Ltd, and funded by the Scottish Government as part of the QMS Strengthening Labels (Pig Resource Use Efficiency) Programme.
“Scottish pig producers operate in a very tight commercial environment, and production is costly due to location and climate,” said Allan Ward, QMS Pig Specialist.
“Producers are constantly looking for opportunities to improve efficiency, and this report highlights a number of areas of potential opportunity to lower pig farms’ annual energy bills,” Mr Ward.
The QMS study included a questionnaire, which was sent to pig units identified as having home mills and doing on-farm mixing. The results reveal that around 86% of the QMS-assured Scottish sow herd and 84% of all pigs from weaning to finishing are fed from feed prepared on the home farms, using produce mostly sourced from the home farm or locally.
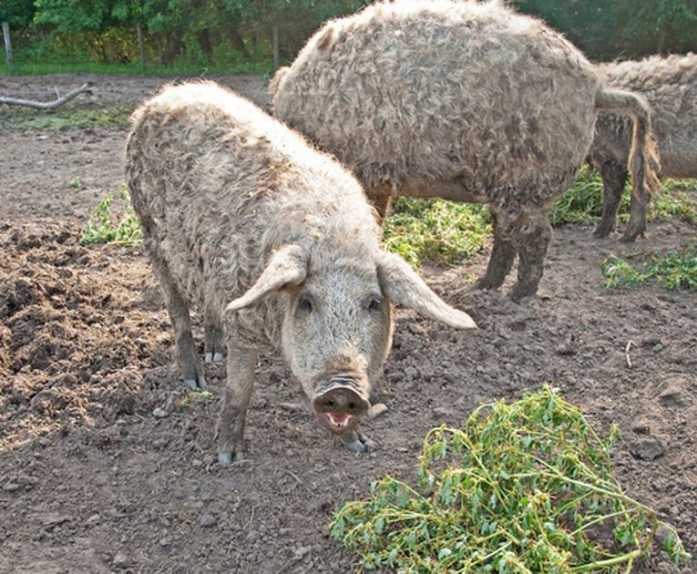
In total, around 74% of sow feed (30,500 tonnes per annum) on QMS-assured Scottish pig units is home milled and mixed, along with 70% (73,800 tonnes per annum) of weaning to finishing diets.
The producer survey revealed a 3.19p/unit difference in the daytime tariff rates paid by producers using more than 100,000 units of electricity per annum.
“The lowest unit consumer was paying the highest price per unit, but thereafter the range of prices paid for a unit consuming more than 100,000 units was 10.31p/unit to 13.5p/unit. This price per unit spread is worth £3,190 per 100,000 unit consumption,” said Rod McGovern of Farm Energy Consulting Ltd.
Among the measures which producers could consider to reduce the energy use associated with feed milling and mixing on their farms were steps to ensure they secure the best tariffs – either by the use of energy brokers/advisers or by researching contract options themselves, ahead of the contract end date.
“One key area of opportunity we identified was the potential to introduce automation of milling so that it is done at night. This could reduce related energy costs by about 40%,” said Jamie Robertson of Livestock Management Systems.
“Not all farms had a split tariff giving a cheaper rate at night compared with daytime, but those who have this arrangement are paying about 40% less for their night rate power than for their daytime power.”
Farm feed mill and mix is consuming from 10% to 38% of whole farm annual electricity consumption. Most feed mills are operated every day for five to eight hours, mostly during the day. One farm operates the mill twice per week for eight hours a day in each case, with farm mills for wet feeding systems working on and off 24 hours per day. Operation at night, however, was limited.
The study also involved feed mills being monitored on five farms to assess their energy use. The results show that the average power used to produce each tonne of feed was 11kW. The results of this small study suggest that more power is used with smaller screen size.
The benefit of maintaining equipment to ensure it operates efficiently was also highlighted in the report. A variety of feed mills are used on Scottish units, ranging from 5.5kW to 40kW power rating. Mills are predominantly hammer mills, though some units use disc mills alone or in parallel with the hammer mills.
Renewing the hammers and screen on a mill reduced the energy used per kilogram of grain by 3% and increased milling rate (kg/m) by 5%. Feed grist size distribution was improved.
On one of the farms the fan in the hammer mill was replaced following the test, resulting in a marked increase in throughput.