SOUTH AFRICA’S Amalgamated Beverage Industries (ABI), Africa’s biggest bottler and producer of Coca-Cola products, has greatly reduced water- and energy-use in a five-year efficiency drive.
ABI, a subsidiary of SABMiller, sells 150m cases (a case is 24 bottles) of Coca-Cola brand products annually and has a 91% share of the soft drinks market in Africa. Producing 1 l of Coca-Cola now requires 1.77 l of water, compared to 2.5 l in 2008, a drop of 30%. Energy use has now dropped 56%. In 2008, producing 1 l of Coca-Cola required 0.495 MJ of energy. Now, the process uses 0.22 MJ of energy.
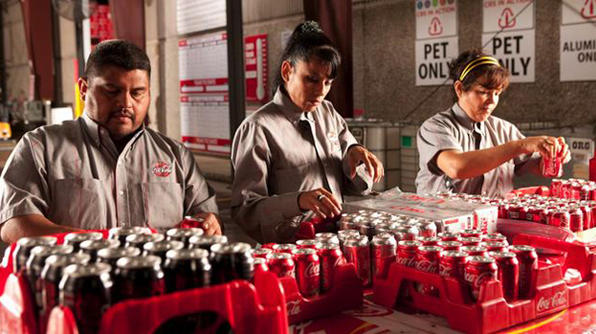
ABI technical manager JP Blumenthal tells tce that the water savings have come from other water recovery systems and water usage minimisation. Rinse water from PET bottles, the glass bottle washer and the plant is now recovered. Some is used in lower specification areas, such as floor washing. Any water fed back into the process goes through several treatment processes, including reverse osmosis where necessary, to ensure it meets Coca-Cola’s standards. Even in delivery truck washing bays, water is recovered and used several times. ABI has also improved the efficiency of its hygiene processes and optimised cleaning processes through using automation to give consistency.
Some energy savings have been made by introducing sensor-controlled lighting and skylights in the roofs to allow more light into plant buildings. However, the large drop in energy use has largely been achieved by reducing the blowing pressure used for moulding bottles. Blumenthal says that across four factories, ABI has 11 lines and 83 sets of moulds. The industry standard pressure ranges from 28–35 bar, with some using high-pressure networks at 35–38 bar. ABI now has several lines running at 22–25 bar. Eventually, all lines with run at 20–25 bar. The company already has 70% of the necessary equipment, with the rest on order for this year.
In addition, ABI will now use a minimum of 20% of recycled PET resin in its bottles, with a medium-term goal to increase this to 30% and a long-term goal of 40% recycled PET. ABI has signed a seven-year PET supply deal with M-Pact, which is building a new PET recycling plant, which will divert 29,000 t/y of the plastic from landfill.
“We have agreed a seven-year pricing model with M-Pact that protects them if the virgin resin price drops too low and shares the benefits as the virgin price increases,” Blumenthal tells tce.
He adds that while the total monetary savings from reducing energy and water use are low relative to the total cost of the product, it is a high priority in terms of the company’s energy footprint and its drive to increase productivity.
Huong Truong