The US Department of Energy (DOE) released the report “Barriers to Industrial Energy Efficiency,” which was prepared with collaboration from nearly 50 experts, including representatives from industrial associations, combined heat and power (CHP) groups, environmental stewardship organizations, associations of state governmental agencies and federal governmental agencies.
According to the report, industrial end-use energy efficiency includes a broad range of energy-efficient technologies and management practices, which include advanced electric motors and drives, high efficiency boilers, waste heat recovery, energy-efficient lamps and lighting controls, modernization or replacement of process equipment, improved process performance through the use of sensors and controls, and implementation of systematic energy management systems.
* Economic and financial barriers, for example, include such things as:
- Internal competition for capital. Manufacturers often have limited capital available for end-use efficiency projects and frequently require very short payback periods (one to three years).
- Corporate tax structures. US tax policies, such as depreciation periods, the treatment of energy bills, and other provisions can be a deterrent.
- Program planning cycles. There can be a mismatch between industrial planning cycles and utility and state energy efficiency program cycles, which can hinder industrial sites from moving forward with an energy efficiency project.
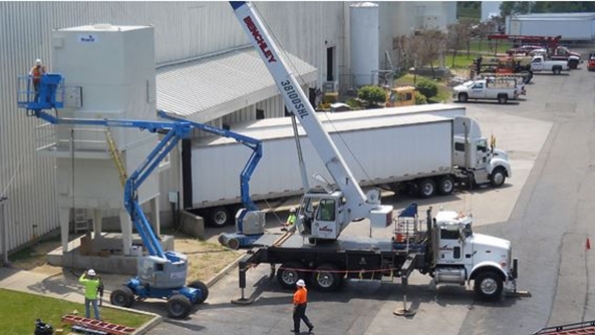
Barriers that impede implementing industrial end-use energy efficiency are found in three categories: i) economic and financial; ii) regulatory; and iii) informational.
- Split incentives. Companies often split costs and benefits for energy efficiency projects between business units, which complicates decision-making.
- Failure to recognize non-energy benefits of efficiency. Not considering non-energy or co-benefits of an end-use energy efficiency project weakens the business case.
- Energy price trends. Volatile energy prices can create uncertainty in investment returns, leading to delayed decisions on energy efficiency projects.
* Regulatory Barriers:
- Utility business model. The structure of utility cost recovery and lost revenue mechanisms can reduce a utility’s interest in promoting industrial energy efficiencyprojects.
- Industrial participation in ratepayer-funded energy efficiency programs. Opt-out programs or loosely defined self-direct programs allow industrial customers to not participate in traditional energy efficiency programs.
- Failure to recognize all energy and non-energy benefits of efficiency. There can beunrecognized energy benefits and non-energy societal benefits associated with improving energy efficiency. If these benefits are omitted, there can be underprocurement of industrial energy efficiency resources.
- Energy resource planning. Not requiring cost-effective energy efficiency to be considered as part of the integrated resource planning process can slow the evolution or expansion of industrial energy efficiency programs.
- Environmental permitting. Uncertainty, complexity, and costs associated with permitting processes such as New Source Review can deter facilities from moving forward with energy efficiency projects.
* Informational Barriers
- Adoption of systematic energy management system. Some manufacturing plants lack information on the benefits of modern energy management systems. These plants fail to capture the value of cost-effective energy savings that can be achieved by these systems.
- Awareness of incentives and risk. Lack of knowledge of available Federal, state and utility incentives for end-use efficiency measures can lead to missed opportunities.
- Metering and energy consumption data. Lack of disaggregated energy consumption data, such as process unit and equipment-level energy consumption data, and tools to evaluate such data, can prevent identification and evaluation of opportunities.
- In-house technical expertise. Lack of in-house technical expertise or the resources to hire outside staff for the development and operation of end-use efficiency projects can hinder deployment.
Truong Duy