A line improvement programme undertaken by Sidel at Japan’s Kirin Distillery has resulted in a substantial saving in the use of electrical energy. Sidel, the leading global provider of PET solutions for liquid packaging, carried out a modular upgrade of the production line and fitted its ECO lamps to the blow moulder on the water line at the distillery, providing a balance of cost and sustainability benefits.
The whisky distillery, which currently holds the record for being the world’s largest, is located in the town of Gotemba at the foot of Japan’s iconic Mount Fuji. The site was selected because it was felt that Gotemba has a climate most like that of Scotland, the birthplace of whisky. With an average annual temperature of only 13°C, it is cooler and more humid than other parts of Japan - especially in summer.
The Kirin facility is one of 10 whisky distilleries in Japan and its production water is taken directly from underground streams flowing beneath the mountain. Unlike most other whisky distilleries throughout the world, the Kirin Distillery undertakes every production process, from mashing to bottling, on-site. It covers a massive 520,000m2 and has an annual production capacity of 12 million litres of four types of whiskies comprising one malt and three grain whiskies. Recognising the opportunities that the underground streams provide for also marketing bottled water, in 1999 Kirin installed a dedicated Sidel PET bottle blowing line and it is this line on which the modular upgrade has been completed.
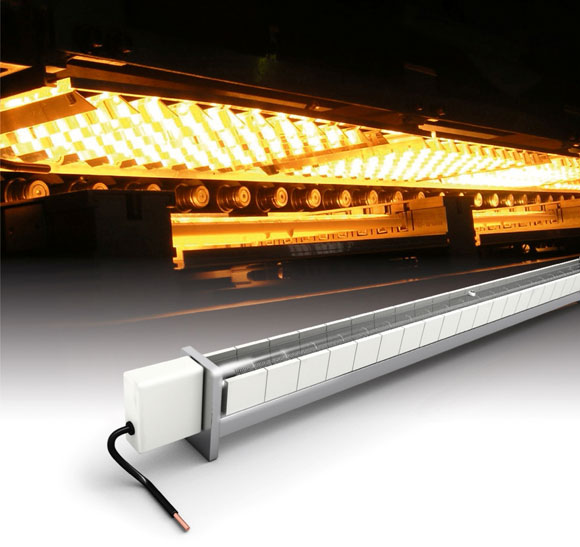
With the increasing environmental consciousness of consumers, sustainable packaging and the renewability of water sources are important factors in the bottled water market. In 2013 total volume sales of bottled water in Japan grew by 4 per cent to reach 4.4 billion litres. From 2013 to 2018, the total market for bottled water in the country is forecast to grow by a CAGR (compound annual growth rate) of 0.7 per cent in value terms, with still bottled water increasing by 0.3 per cent CAGR.
The Project Manager at the Kirin Distillery says: “Kirin selected Sidel's ECO lamps to be fitted to its existing PET water line in its continuous search for greater sustainability and cost effectiveness.
The lamps have generated substantial energy savings and have also brought the benefits of improved process stability and optimised production output.”
There is a growing need within the beverage industry to balance economic performance with environmental concerns and reducing greenhouse gas emissions is an integral part of the process. With the heating lamps used to produce preforms accounting for 90-95 per cent of the electricity used by a blow moulder, Sidel ECO lamps have been developed based on a seemingly simple concept that addresses these concerns. Since their launch in 2008, Sidel's ECO lamps have been meeting customers' requirements providing an effective solution which is easy to install. Available as a modular upgrade of beverage production lines on both the Sidel SBO Series 1 and Series 2 blowers, ECO lamps generally result in energy savings of around 15 per cent. In some cases, installation requires no modification to either the existing oven or the blowing process. As well as reducing energy consumption, Sidel's ECO lamps are robust and have a life expectancy of 5,000 hours.
Moriyasu Uchibori, lead Customer Service Manager of Sidel, Japan, explains: “With electricity costs still rising globally and the growing drive to reduce CO2 emissions, producers around the world are looking to optimise productivity and minimise the total cost of ownership on all their lines. In a typical line, preform heating lamps are clearly an area with potential for greater energy efficiency. Sidel’s ECO lamps represent one way in which both energy and money can be saved.”
Truong Duy