When you decide to invest in an energy efficiency upgrade at your industrial facility, how do you verify that you’re actually getting the savings you were promised with new equipment or optimization?
With highly specialized equipment and processes, determining the energy savings from an equipment upgrade is much more complicated than a simple “before and after” calculation using your monthly utility bill. However, this is the approach many plant managers take when it comes to energy efficiency. Doing measurement and verification (M&V) exclusively with your utility bills doesn’t just put you at risk of overstating savings, you also risk understating them dramatically.
Installations don’t always go as planned and factors like occupancy, temperature, production volume, and changing rate classes can make calculating accurate savings difficult. Efficiency also erodes over time, so if you want to lock in savings for the long term, M&V is an extremely critical step for your efficiency investment. In fact, according to Lawrence Berkeley National Laboratory, each year 20% of savings achieved through a full-scale retro-commissioning effort erode, which means that in five years, you’re back to square one.
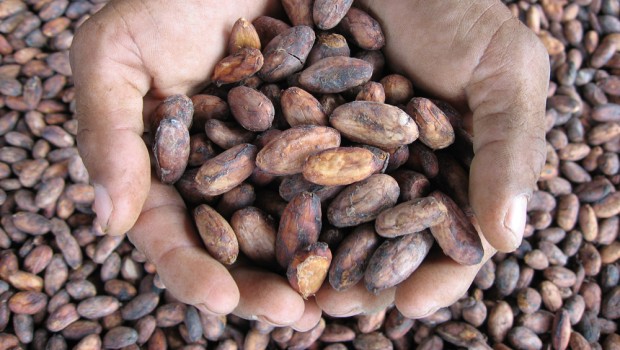
Eric Bliss, Senior Engineering Manager for Blommer Chocolate Company, the largest cocoa processor and ingredient chocolate supplier in North America, knows the importance of M&V all too well.
At one of his plants, Bliss replaced a chiller with a more efficient unit, carefully projecting ROI and monthly savings before they approved the project. But the team didn’t see the expected reduction in their utility bill.
When the team originally calculated the expected savings, they didn’t factor in that the plant was growing, which meant it was consuming more energy month over month. The only way Bliss and his team could see the production-adjusted effect of the new was by using energy intelligence software (EIS).
“The chiller replacement was actually successful and did generate savings, but they weren’t immediately visible because we didn’t have access to our real-time energy data,” said Bliss. “Another plant with the real-time data also replaced chillers for efficiency savings, and as a result, we were able to weed out the volume effect on daily consumption to show savings of over $300,000.”
Bliss knows how important it is to treat energy the same way he manages Blommer Chocolate’s other operations and processes. “Energy is not rent, it’s actually more like an ingredient, with consumption directly correlated to production,” Bliss explained. “It’s actual, manageable cost.”
Truong Duy