Energy efficiency and conservation measures at Van Dien Fused Magnesium Phosphated JSC
Chủ nhật, 13/10/2024 - 10:18
In July 2024, Van Dien Fused Magnesium Phosphate JSC conducted an energy audit. Energy audit experts assisted the company in identifying the optimal solutions for further energy-saving implementations.
Mr. Pham Quang Trung, Deputy General Director in charge of production technology at Van Dien Fused Magnesium Phosphate JSC, shared that the company has an annual capacity of 300,000 tons of fused phosphate fertilizer and 150,000 tons of NPK compound fertilizer. Due to the specific production technology using high-temperature kilns to process natural mineral ores into fertilizer products, the company consumes approximately 50,000 tons of coal, 10 million kWh of electricity, and 350 tons of various fuels annually to produce fertilizers for the market. These energy and fuel costs are substantial, accounting for about 40% of the product's production cost. Therefore, energy saving is crucial for enhancing production efficiency and environmental protection.
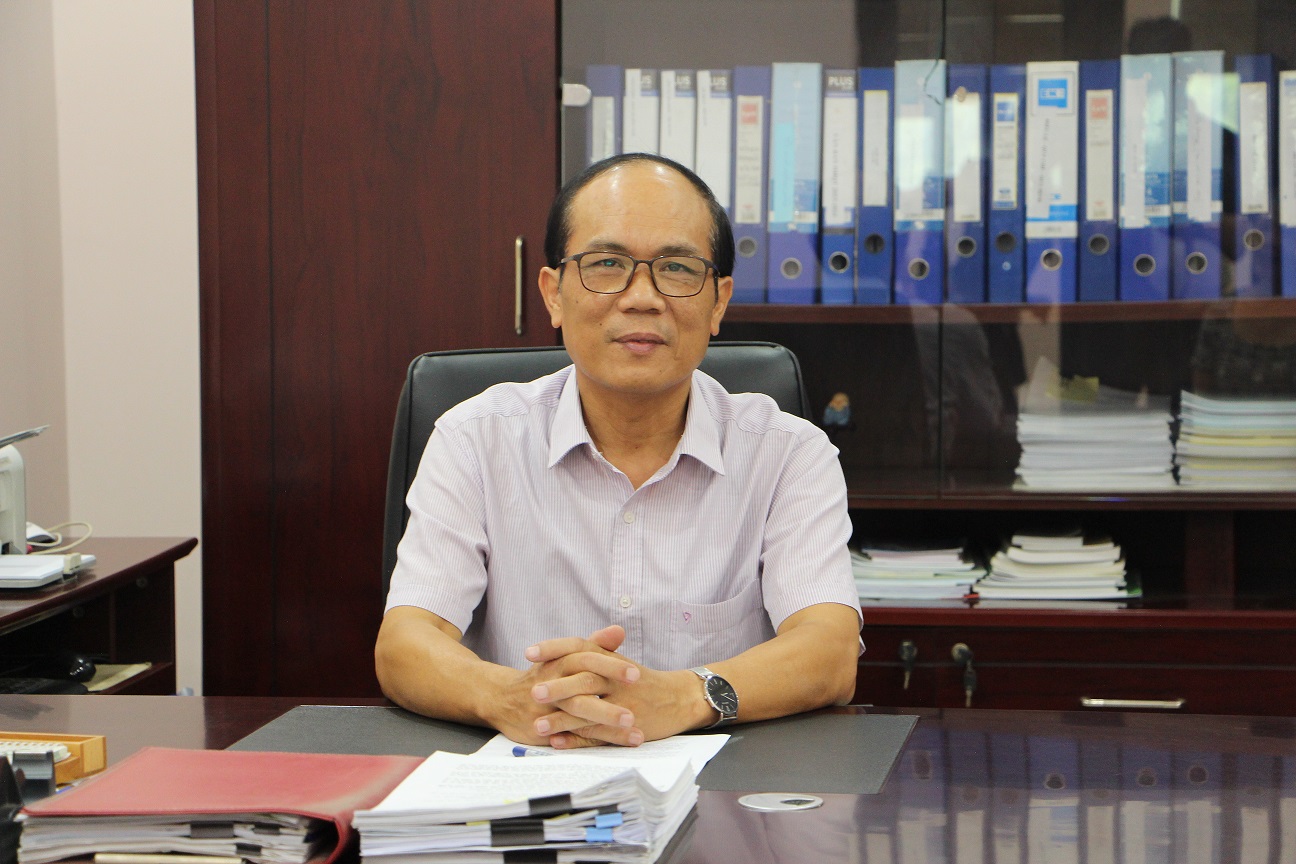
Mr. Pham Quang Trung, Deputy General Director manages production technology at Van Dien Fused Magnesium Phosphate Fertilizer Joint Stock Company.
Since the implementation of the Law on Economical and Efficient Use of Energy, along with the guiding Decrees and Circulars from various ministries, the company has established an Energy Management Board, conducted periodic energy audits every three years, and developed annual and five-year plans to implement energy-saving measures.
"Through various energy audits, the company collaborates to review and identify priority areas with high potential for energy savings to develop implementation plans. In July 2024, the company conducted an energy audit organized by the Ministry of Industry and Trade in coordination with the Korea Energy Agency. After the energy audit, with the participation of experienced experts from the Ministry of Industry and Trade and Korean partners, we aim to evaluate the entire current energy use status in each area and the main energy-consuming equipment in the company's production activities. Based on the audit results and expert evaluations, the company aims to identify the optimal solutions for further implementing energy-saving measures in the future," said Mr. Pham Quang Trung.
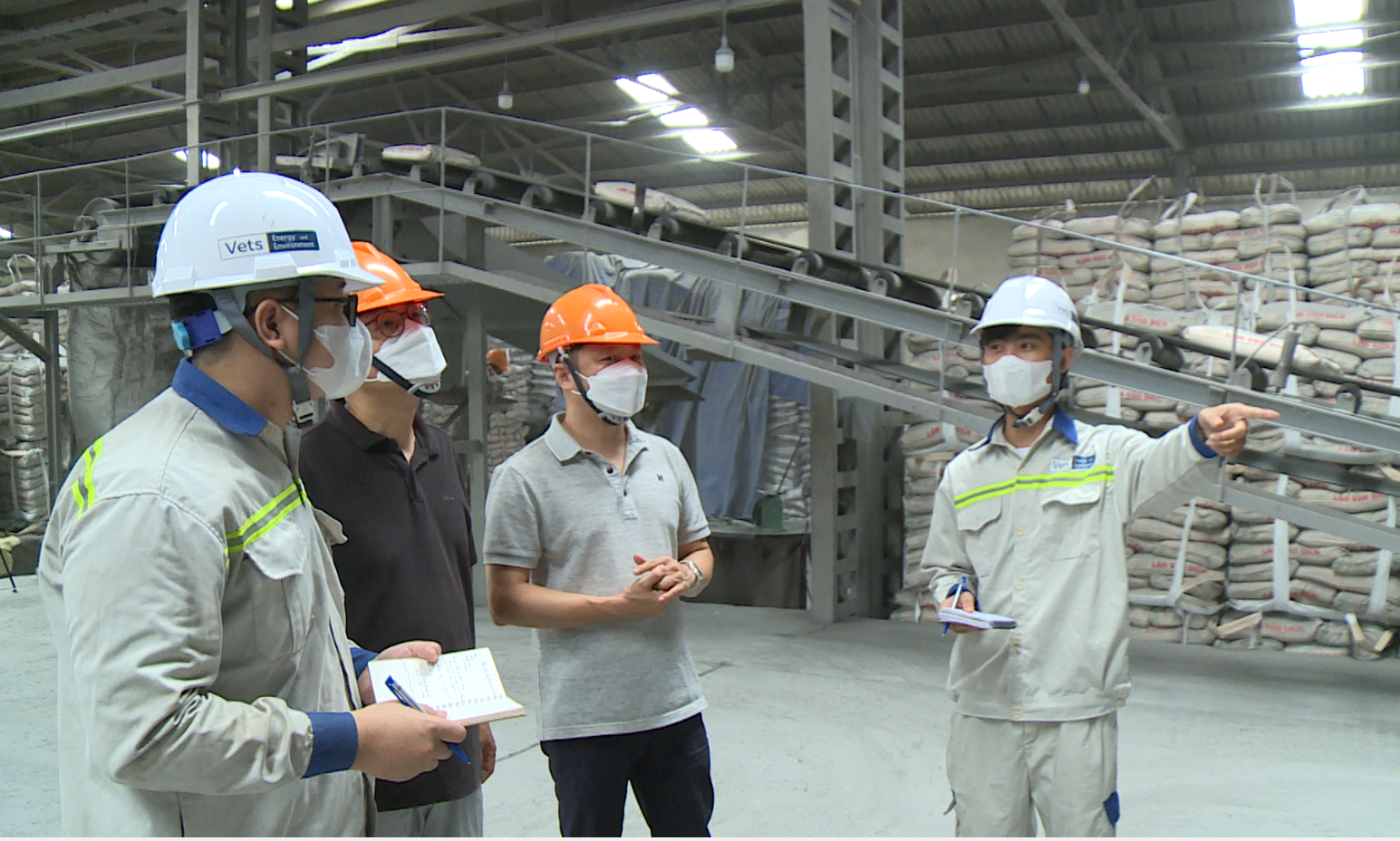
Van Dien Fused Magnesium Phosphate Fertilizer Joint Stock Company Conducts Energy Audit in July 2024.
Over the years, the company has consistently focused on and maintained a policy of researching and applying scientific and technological solutions for sustainable and environmentally friendly development. The company also emphasizes the importance of training and raising awareness among its staff to ensure energy-saving objectives are met. Annually, the company plans to send specialized staff to energy-saving training courses to enhance their knowledge, which they then disseminate to all employees to promote efficient energy use.
Additionally, the company has continuously invested in technological innovations, production line improvements, and the application of science and technology to reduce raw material and energy consumption, as well as emissions.
Mr. Dinh Tuan Hai, Deputy Head of the Technical Department in charge of energy at Van Dien, stated: "To save energy, the company has implemented several energy-saving and efficiency measures, specifically: enhancing management practices, organizing production efficiently, upgrading technology and adjusting the capacity of some motors and equipment to match their functions, modifying speed reducer structures to minimize power losses, and installing power factor correction capacitors near the load to reduce line losses (saving 1.5-2.5 kWh per ton of product compared to standard levels).
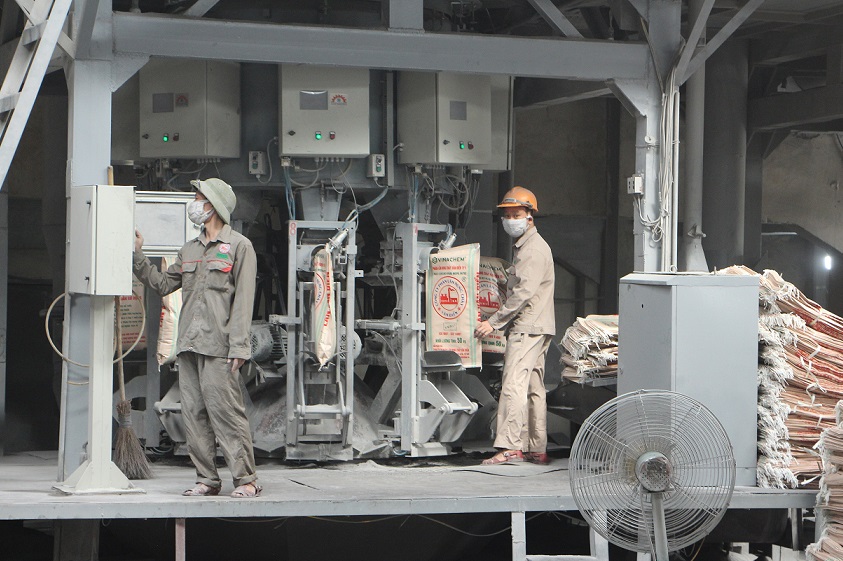
Product Packaging Line.
For the lighting system, the company has replaced 100% of Halogen bulbs (500-1,000W), high-pressure mercury lamps (250-400W), incandescent bulbs (40-100W), T5, T8, T10 fluorescent tubes (20-40W), compact fluorescent bulbs (50W), etc., with energy-saving LED bulbs (100W, 30W, 18W, 12W, 9W).
Additionally, the company has strengthened management efforts and researched technological improvements and high furnace equipment to reduce coal consumption standards (saving 3-5 kg of coal per ton of product compared to the standard). It has also enhanced the management of vehicles; established regular and periodic maintenance plans; and reduced fuel consumption (saving 8-10% of the oil used compared to the standard).
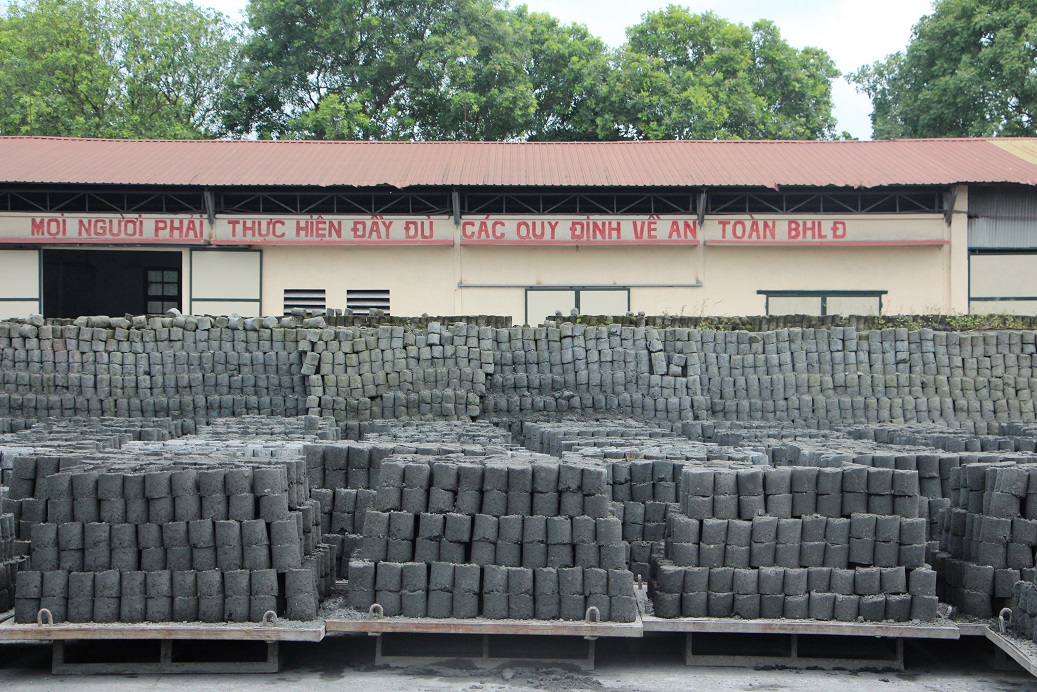
Fine raw materials are generated into Ab bricks and reused as production materials.
Sharing about the recycling solution to save raw materials, Mr. Hai stated that the company has researched technology and additives for briquette ore, reusing 100% of undersized raw materials to produce fused phosphate fertilizer, recovering about 50,000 - 60,000 tons of fine ore per year, eliminating solid waste, and saving 15-20% of raw materials annually.
The company has implemented a scientific project titled "Research on Wastewater Recycling." Since 2016, 100% of industrial and domestic wastewater, after treatment, has been returned to production; saving approximately 4-5 million cubic meters of water resources, over 500,000 kWh of electricity, recovering about 3,500 tons of semi-finished products, avoiding environmental fees, and eliminating wastewater, bringing in benefits of over 10 billion VND annually.
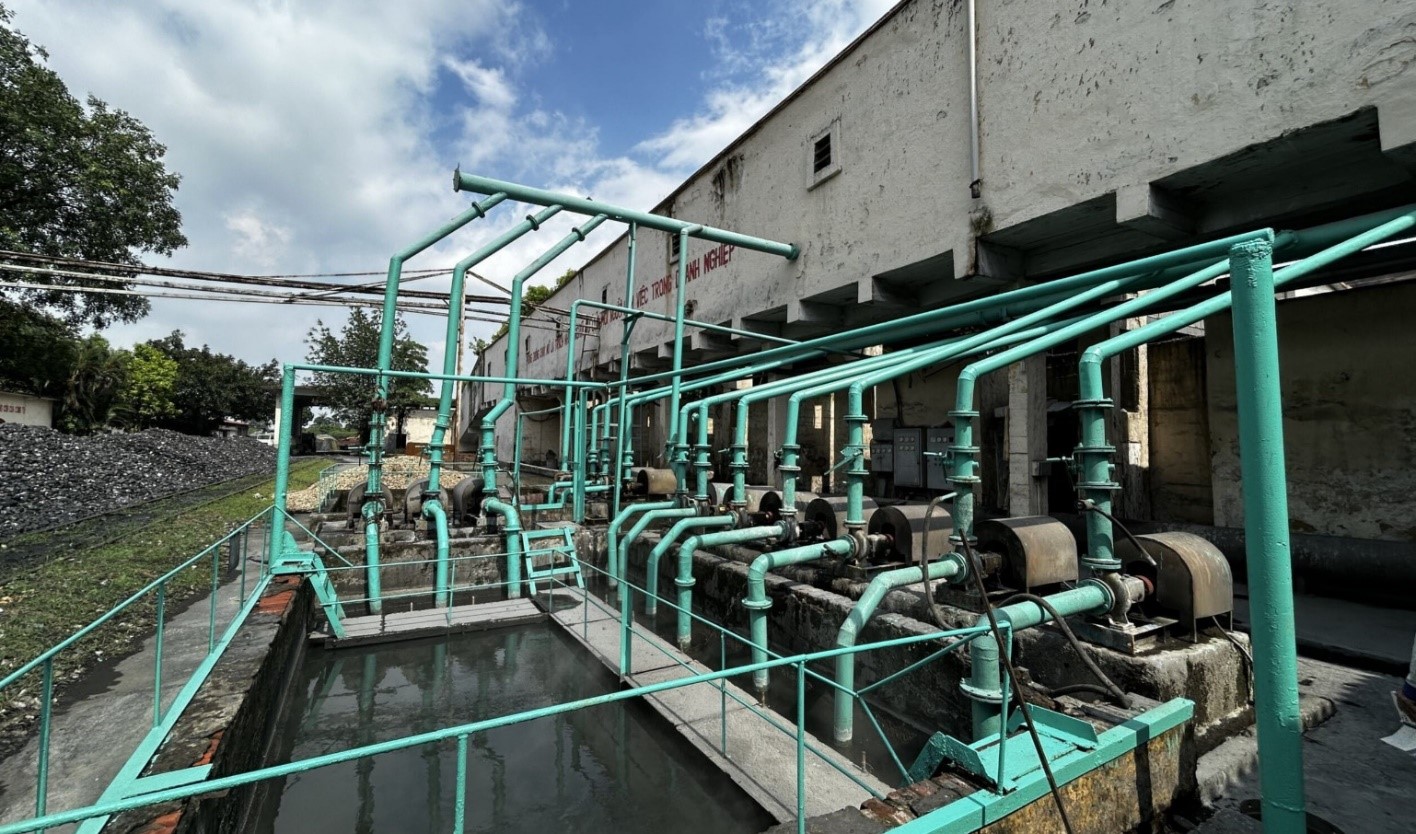
Production wastewater is treated and recycled 100%.
Thanks to the application of energy-saving measures, Van Dien Fused Magnesium Phosphate Fertilizer Joint Stock Company has gained significant economic benefits, increasing the competitiveness of its products. In the future, the company will continue to research, review, and apply technical solutions to reduce electricity, coal, and oil consumption per ton of various products.
Duc Do