Energy Efficiency in Cement Production
Thứ hai, 21/10/2024 - 14:22
Cement production is one of the industries with high energy consumption, and cement enterprises prioritize finding effective energy-saving solutions to reduce costs and increase profits.
Energy Efficiency Potential
It is estimated that electricity costs account for about 10-15% of the total production cost of cement. On average, producing 1 ton of cement consumes more than 100 kWh of electricity.
According to calculations by the Vietnam Energy Association, 75% of the primary energy used in cement production plants is thermal energy, and 1 ton of waste heat can generate 3-5 kWh of electricity. If all cement plants utilize the waste heat from clinker kilns to generate electricity, it could result in approximately 1.5 billion kWh of electricity savings annually.
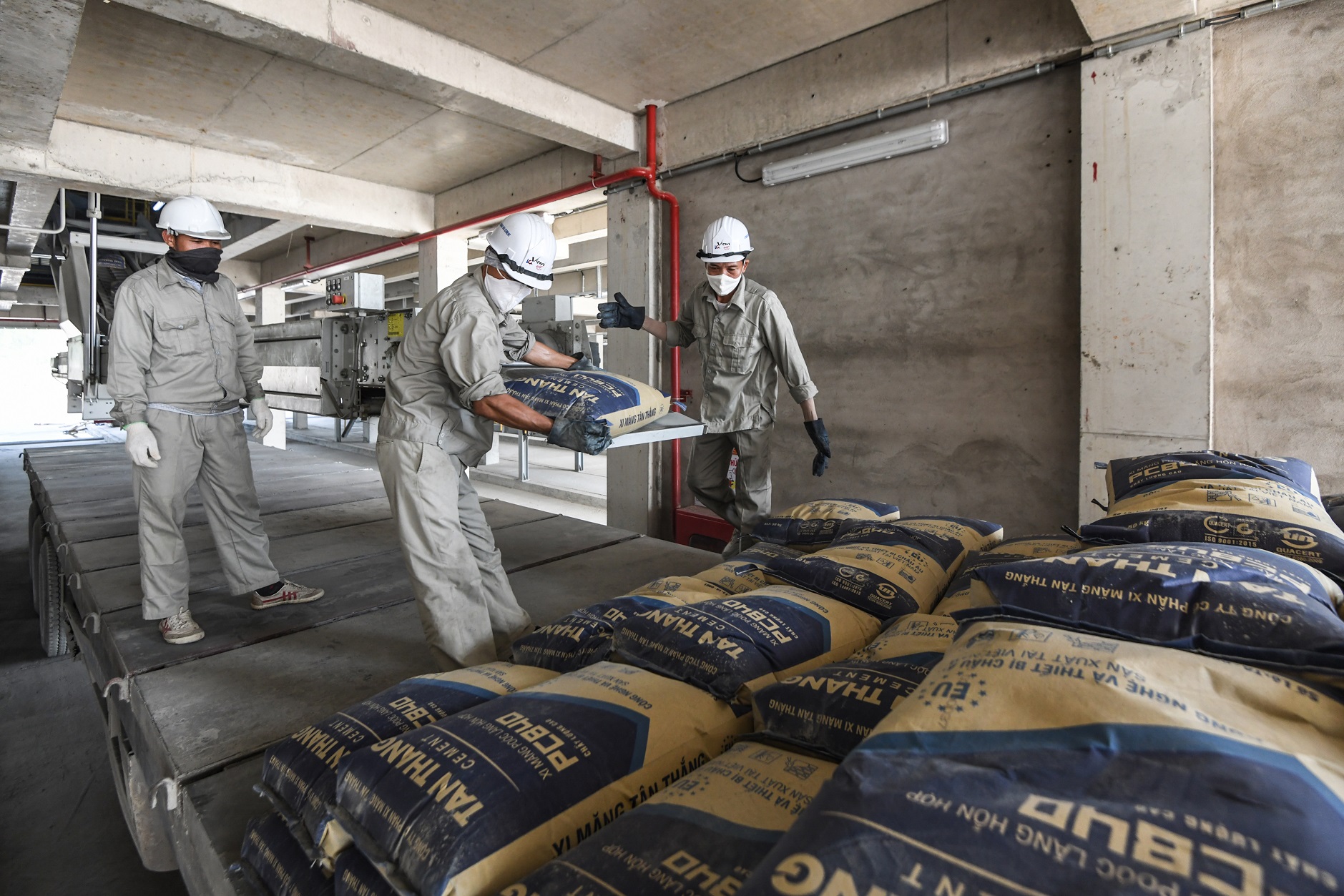
Saving energy to reduce costs and increase profits is always a concern for cement manufacturing enterprises.
Energy-saving solutions in cement production can generate up to 30% of a plant's electricity demand. This prevents energy waste and helps reduce dust and emissions, contributing to environmental protection.
Additionally, the European Union’s (EU) Carbon Border Adjustment Mechanism (CBAM), set to be enforced from January 1, 2026, will require Vietnamese companies, including cement producers, to shift toward greener production methods, saving resources and energy, and reduce greenhouse gas emissions.
Faced with the increasing demand for efficient energy use, many cement enterprises have actively adopted energy-saving technologies and solutions, which help reduce environmental impacts and improve production efficiency.
Proactive Energy Savings by Enterprises
In cement production plants, energy consumption, particularly electricity, accounts for a significant portion of production costs. Efficient and economical use of electricity helps reduce production costs, lower product prices, and increase market competitiveness.
Quan Trieu Cement Joint Stock Company is one such enterprise that actively seeks technological solutions for energy savings and cost reductions.
Over the years, the company has implemented several improvements to its production equipment across various stages, such as: Replacing older coal-burning equipment with new, more efficient models to save energy during clinker firing; Upgrading raw material grinders to improve productivity and save electricity; Utilizing alternative materials such as fly ash from thermal power plants as additives in cement; Using grinding aids to enhance product quality and production efficiency.
Over the years, the company has implemented several improvements to its production equipment across various stages, such as: Replacing older coal-burning equipment with new, more efficient models to save energy during clinker firing; Upgrading raw material grinders to improve productivity and save electricity; Utilizing alternative materials such as fly ash from thermal power plants as additives in cement; Using grinding aids to enhance product quality and production efficiency.
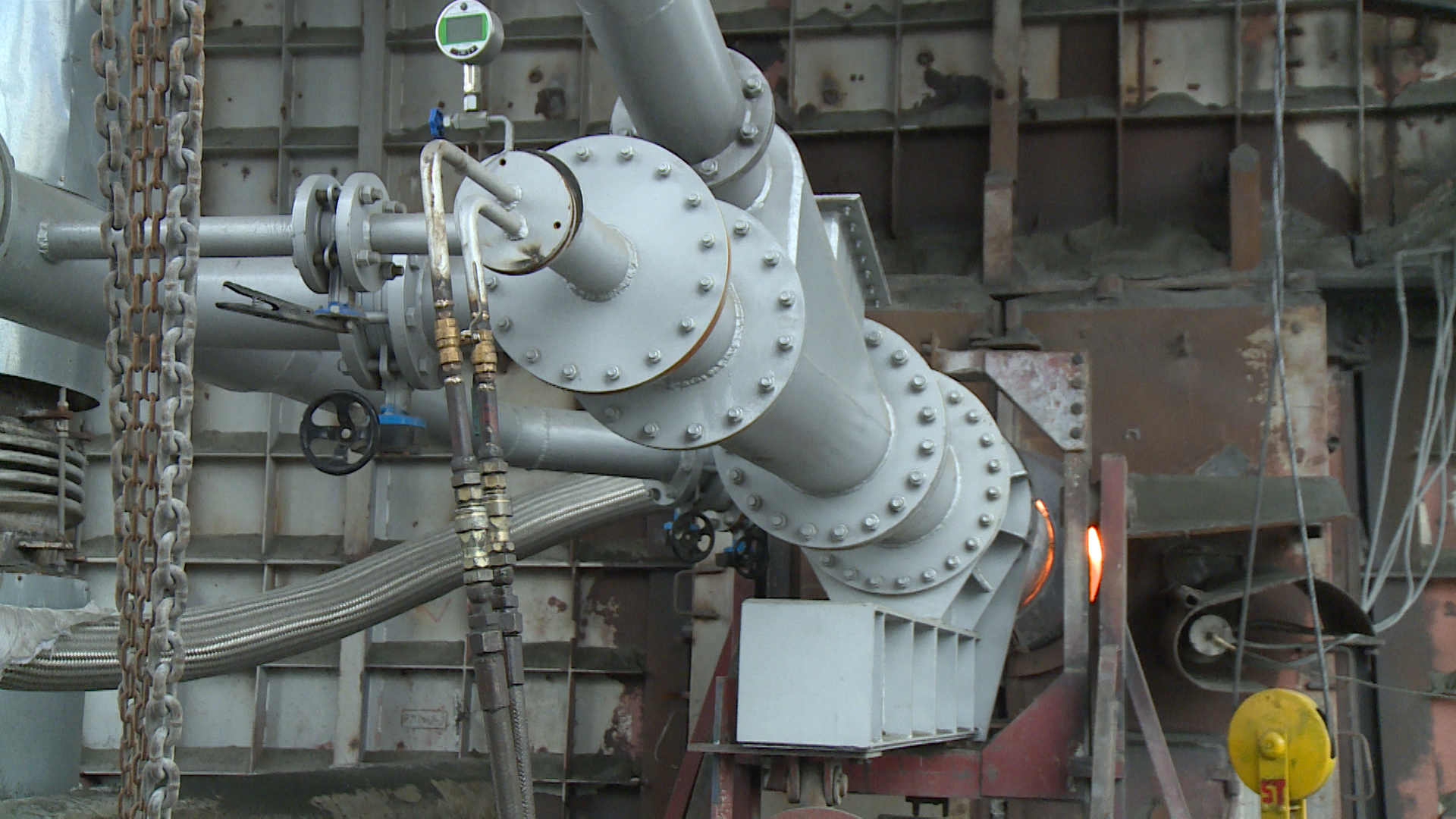
Production Line at Quan Trieu Cement Plant.
According to Mr. Dao Trung Dung, Deputy Technical Director of Quan Trieu Cement Joint Stock Company, Quan Trieu operates the only production line in Vietnam and the world that uses limestone from coal mining processes as its primary raw material. This use of limestone-containing coal has allowed the company to reduce its thermal energy consumption significantly.
Mr. Dung revealed, "Typically, cement plants under the Vietnam Cement Industry Corporation (VICEM) consume about 720 - 750 kCal/kg of clinker, but Quán Triều Cement only consumes around 600 kCal/kg, saving approximately 120 - 150 kCal per kilogram of clinker."
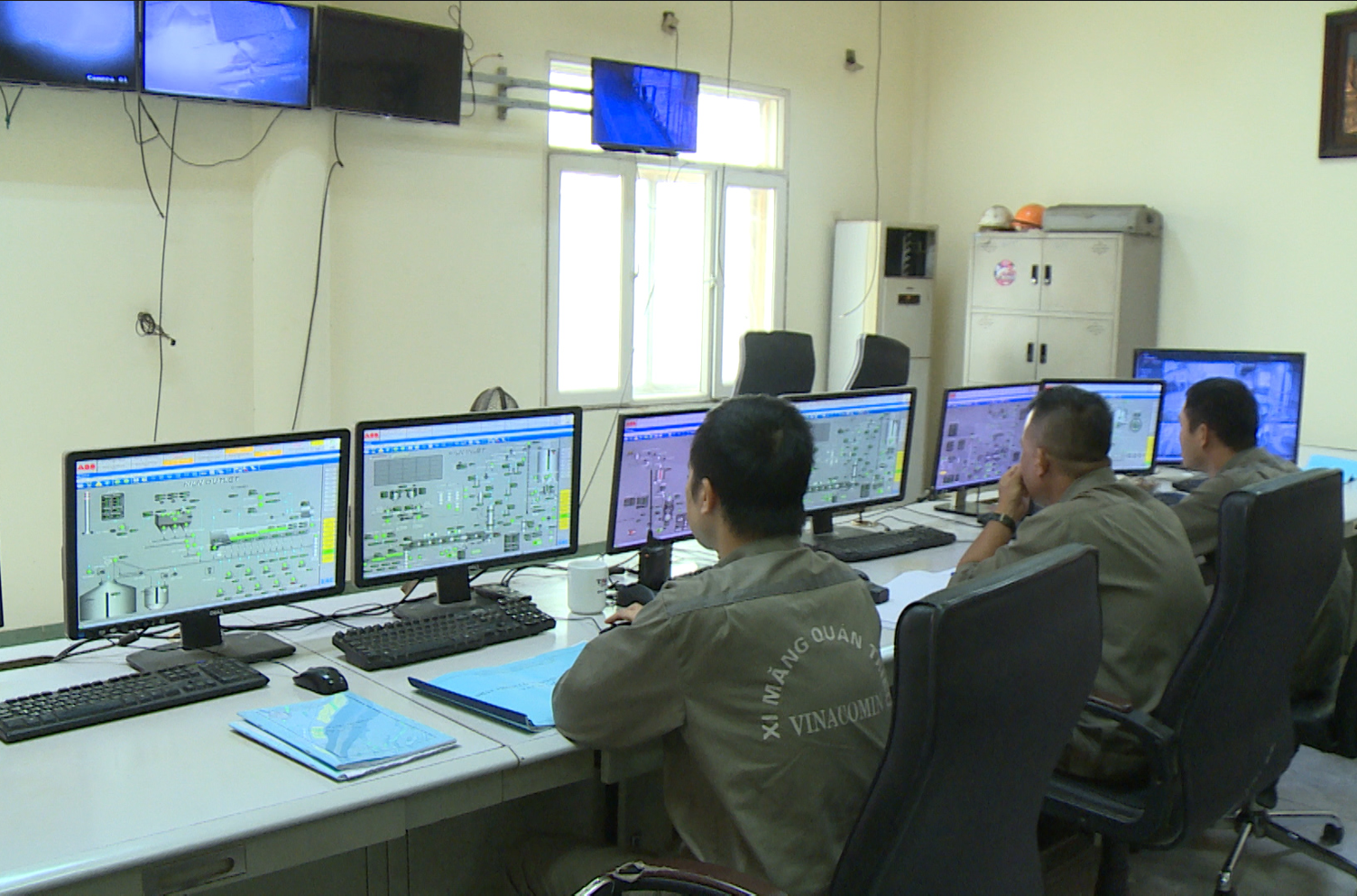
Production Monitoring at Quan Trieu Cement.
Discussing future energy-saving solutions, Mr. Dung shared that the plant is currently surveying and planning to install a waste heat recovery system. This system would capture hot gases emitted during the clinker burning and cooling processes to generate electricity. It is estimated that once installed, the waste heat recovery system could supply about 30% of the plant's electricity needs.
According to Mr. Hoang Huu Tan, Deputy Director of the Department of Building Materials, Ministry of Construction, since 2011, many cement manufacturers have implemented various energy-saving measures. Notably, cement production lines have been equipped with waste heat recovery systems to generate electricity, which can save around 25% – 30% of the electricity used in production. To date, 34 cement production lines nationwide have implemented waste heat recovery systems with a total electricity generation capacity of 247 MW. Sixteen more production lines are being developed with an expected combined capacity of 80 MW. Some cement plants have even invested in solar power systems within their premises to further support electricity generation. In addition to these efforts, many cement plants have been investing in co-processing systems to handle industrial, agricultural, and municipal waste (such as rice husks and cashew shells), reducing fuel (coal) usage and protecting the environment. |
Xuan Thanh Cement Joint Stock Company has invested over VND 450 billion in a waste heat recovery power station with a capacity of 24.8 MW.
Mr. Vu Quang Bac, General Director of Xuan Thanh Cement, stated that the plant operates at about 80 - 90% capacity for waste heat recovery, with the remaining heat used for drying materials in the raw and coal mills. This system helps recover heat from the preheater tower and kiln to generate electricity, with a capacity of 22 - 23 MW, providing over 30% of the plant's total electricity needs.
“Typically, cement production emits a certain amount of exhaust gases, but with this technology, the waste heat is captured and converted into electricity. Utilizing waste heat in cement production brings tremendous economic benefits, helping the plant save around VND 20 billion on electricity costs each month,” Mr. Bac noted.
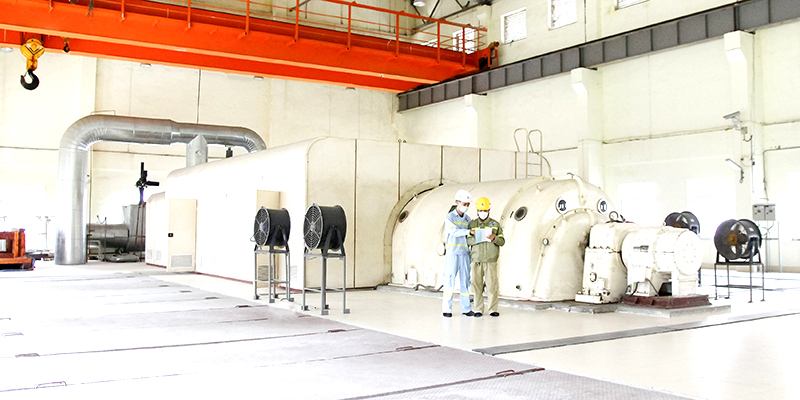
Xuan Thanh Cement's residual heat generation system helps save up to 30% of energy for the factory.
Xuan Thanh Cement has implemented a series of energy-saving solutions, including: Installing inverters for cooling fans in the kiln shell, mechanical workshop overhead cranes, and Ecrane grease pumps; Installing inverters for CL12 and CL13 fans on the DC1 grate cooler fan; Installing power control devices for bucket elevator motors FM7M and FM47M; Installing voltage control systems for silo material aeration fans; Modifying and utilizing phase advance systems for 6kV motors, RM24 motors (2,000 kW), and FM41 motors (3,550 kW); Adjusting the temperature across all power stations from 20±2°C to 23±2°C; Upgrading the lighting system in production line 2.
Many cement enterprises are increasingly aware of the importance of energy savings. Energy savings equate to cost savings, directly impacting product costs and the competitiveness of the company in the market.
Duc Do