Naturally, energy efficient components lower the customer’s electric bill — every year of the system’s life — and that leads to faster return on investment (ROI), making for an easier sale. But there’s more. Energy-efficient components also create huge opportunities for product innovation, including mobile solutions. And they deliver less downtime, greater system productivity, and longer product life.
What types of components are available in energy-efficient versions? Motors, gearboxes, actuators, sensors, and lighting are some of the energy-efficient components available to original equipment manufacturers (OEMs) and system integrators who develop automation systems.
To learn about the state of energy-efficient components, their benefits, and their cost savings, we spoke to experts at JLC Robotics and MOONS’ Industries.
Energy efficiency enables mobile solutions, less downtime
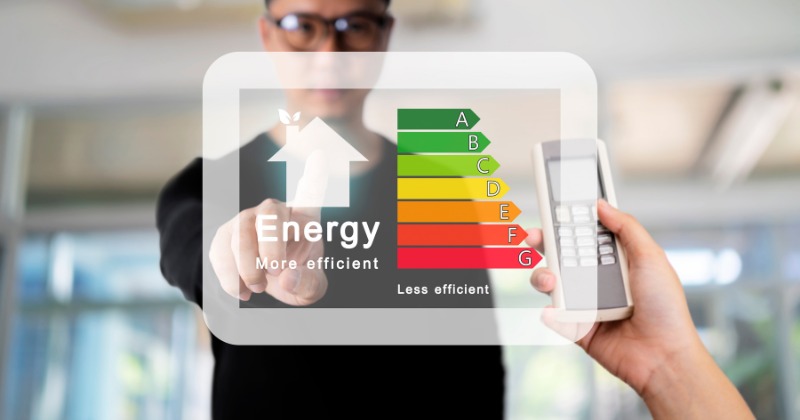
When product engineers and system integrators are able to get energy usage down low enough, opportunities open for battery-power and wireless-power mobile applications that eliminate the need for equipment to be tethered to a power outlet.
But mobile equipment that uses batteries needs to be recharged, and docking and charging time is downtime. “A lot of focus on energy efficiency is driven by the requirements of mobile and battery-powered equipment,” says Andy Sklierenko, vice president of MOON'S industries.
Energy-efficient components enable automated mobile systems, such as autonomous mobile robots (AMRs) and automated guided vehicles (AGVs), to go longer between recharges and spend less time charging. “With energy-efficient components, you save time that would have been spent in returning to the charging station, docking, and recharging,” Sklierenko says. “You get more operational hours, more uptime, and all-around more productivity from automation products when equipment manufacturers focus on energy efficiency, which can result in smaller fleets and lower upfront cost.”
Jamie Callihan, owner of JLC Robotics, an industrial automation distributor, agrees. “We became much more energy-aware when we met with customers with operational layouts that required more solution uptime for AMRs and AGVs. We’ve found that energy-efficient components save costs in several ways. They reduce downtime, extend the lifespan of robotics batteries, and minimize the need for additional power infrastructure.”
A limitation of AMRs is their battery life but docking stations that recharge batteries aren’t the only way to power energy-sipping AMRs and AGVs. On-the-fly wireless charging systems are an option. Callihan explains that in fast-paced environments, such as Tier 1 automotive, warehouse, and logistics, an in-motion energy transfer solution, such as CaPow's Genesis, can enhance automated operations' efficiency. “A key benefit of the use of energy-efficient components in AMRs and AGVs is more uptime, which reduces the size of the fleet required, because productivity is higher. With a perpetual power solution, mobile robot fleets can be charged both at rest and in motion.”
Innovations in motors save energy
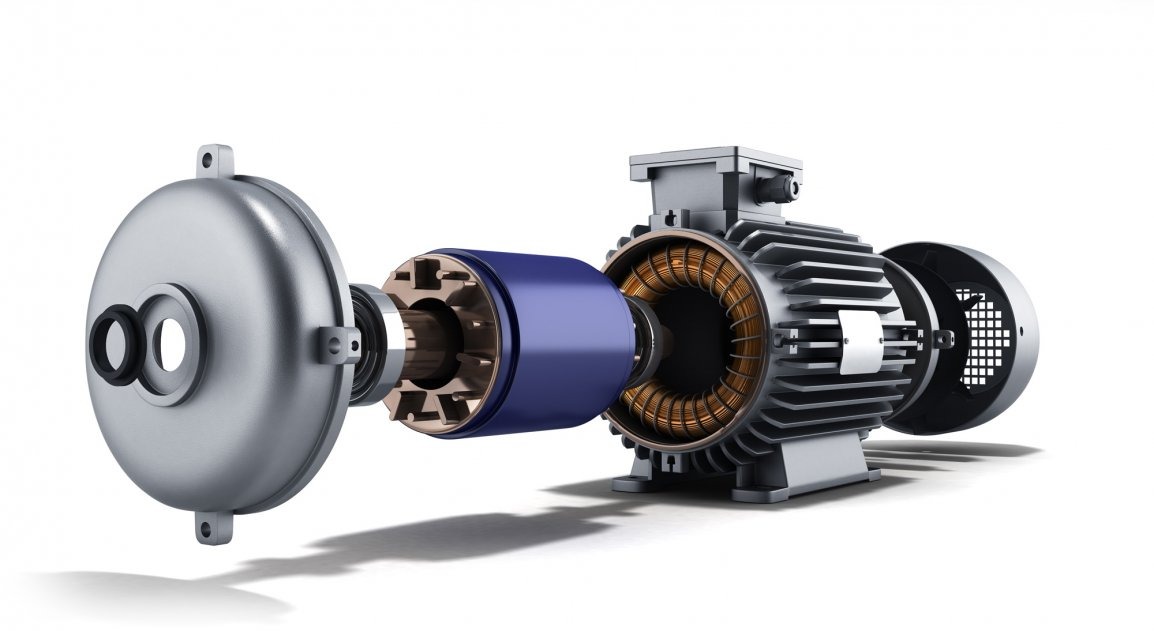
“Given the predominance of motors in industrial processes, improving the energy efficiency of installed motor systems is a key way of increasing industrial technical efficiency,” reports the International Energy Agency (IEA) in "Energy Efficiency 2020".” The report goes on to explain, “Moreover, despite new regulations increasing the efficiency of motors, motor-driven units, such as pumps, fans and compressors, still have limited coverage by minimum energy performance standards and rely on original equipment manufacturers to increase the energy efficiency of their products, depending on their perception of market needs.” Rather than being driven by regulation, the market for energy-efficient motors used in industrial automation is driven by customer demand. Sklierenko describes two popular types of energy-efficient motors — brushless DC (BLDC) motors and slotless BLDC motors — as well as custom motor solutions, high-efficiency gearboxes, and other energy-efficient components, such as actuators.
Brushless DC motors (BLDC) are an increasingly popular type of energy-efficient component, commonly replacing AC motors in heating, ventilation, and air conditioning systems (HVAC), Sklierenko says. BLDC motors use less energy and last longer than motors that use brushes.
Slotless BLDC motors are a type of BLDC motor that is even more efficient. Sklierenko explains that slotless motors eliminate cogging, a source of noise and vibration. As a result, slotless BLDC motors are quieter and last longer.
Custom motor solutions are also available. Adjusting the windings, for example, on a BLDC or stepper motor can change the energy-consumption of a motor. Sklierenko shares a situation in which a manufacturer wanted to produce a machine that would run on a standard electrical circuit. Custom windings enabled the customer to get current draw low enough to meet a design requirement.
The gearbox used to drive a motor also affects energy use. High-efficiency gearboxes are available to transmit the power to drive a motor using less energy.
Other mechanical components, such as actuators, are also available in energy-efficient versions. Energy-efficient actuators can both save energy and reduce undesirable behaviors, such as backdriving and freewheeling.
Machine intelligence makes components more energy efficient
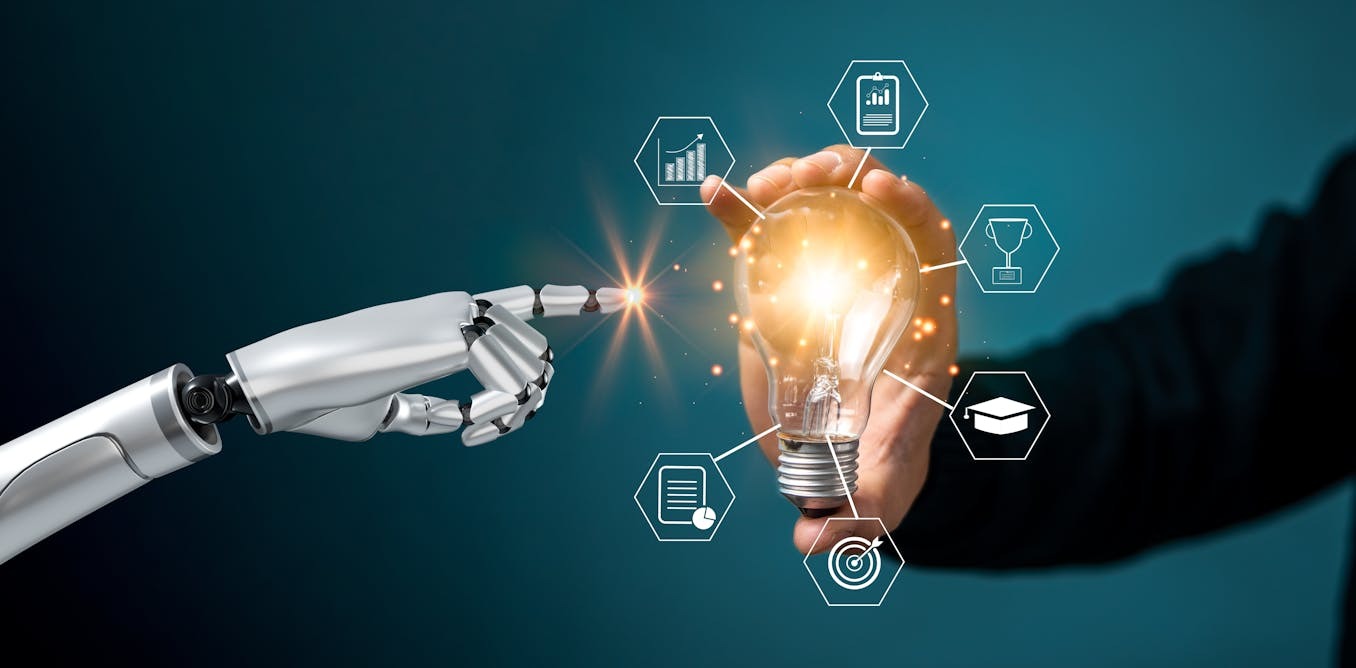
Adding computing capability to mechanical components is another way to achieve energy efficiency. Smart components, such as servo motors, minimize energy waste through the fine control of power delivered to a motor. Artificial intelligence (AI) and machine learning help in other ways, too, such as ensuring maintenance is performed before a component begins to work less efficiently.
Sklierenko explains that intelligent components with closed data-feedback loops adjust power on the fly to use just enough energy to get the job done. A servo motor, for example, has a closed feedback loop at three levels — proportional, integral, and derivative. Proportional control adjusts a motor’s output based on the variation from a setpoint. Integral control adjusts a motor’s output based on accumulated error. And derivative control adjusts a motor’s output based on how fast the amount of error changes. In these ways, servos use AI to run a motor in a more energy-efficient way.
The following video by MOONS’ Industries demonstrates two motors of equal size. One is controlled open loop by a microstepping drive. The other is a step-servo closed-loop integrated motor with a drive encoder and controller. At a fixed speed of 10 revolutions per second and equal loads of 50 ounce-inches, the microstepping motor draws 0.7 amps and consumes 87 watts of power. By contrast, the step-servo closed loop motor draws only 0.4 amps and consumes 50 watts — a 40% power reduction.
Predictive maintenance is another way that AI can reduce energy use. By self-identifying when maintenance is required, an energy-efficient component can help a company avoid energy-wasting situations in which a part starts running hotter or begins to vibrate.
According to automate.org