Energy Efficiency in Food Processing: Strategies for Cutting Costs and Lowering Emissions
Thứ năm, 07/11/2024 - 09:04
The food processing industry is one of the most energy-intensive sectors, consuming vast amounts of electricity and fuel to transform raw ingredients into the products we consume daily. This high energy usage not only contributes to significant operational costs but also results in substantial greenhouse gas (GHG) emissions. Implementing energy-efficient practices is crucial for reducing both costs and environmental impact. This article explores various strategies to enhance energy efficiency in food processing, ultimately leading to a more sustainable and profitable industry.
The Importance of Energy Efficiency in Food Processing
Energy efficiency in food processing is vital for several reasons:
- Cost Reduction: Energy costs can account for a significant portion of a food processor's operating expenses. Improving energy efficiency can lead to substantial cost savings.
- Environmental Impact: Reducing energy consumption lowers GHG emissions, contributing to environmental sustainability and helping combat climate change.
- Regulatory Compliance: Increasingly stringent environmental regulations require food processors to adopt energy-efficient practices to remain compliant.
- Competitive Advantage: Energy-efficient operations can improve a company's market position by reducing costs and enhancing its sustainability credentials.
Key Strategies for Energy Efficiency
- Energy Audits and Monitoring Conduct Energy Audits: Regular energy audits can identify areas of inefficiency and highlight opportunities for improvement. These audits should assess all aspects of the production process, from raw material handling to finished product storage.
- Implement Energy Monitoring Systems: Installing advanced energy monitoring systems can provide real-time data on energy consumption, enabling operators to pinpoint inefficiencies and track progress.
- Efficient Equipment and Technology Upgrade to Energy-Efficient Equipment: Investing in modern, energy-efficient machinery can significantly reduce energy usage. Look for equipment with high energy efficiency ratings, such as Energy Star-certified appliances.
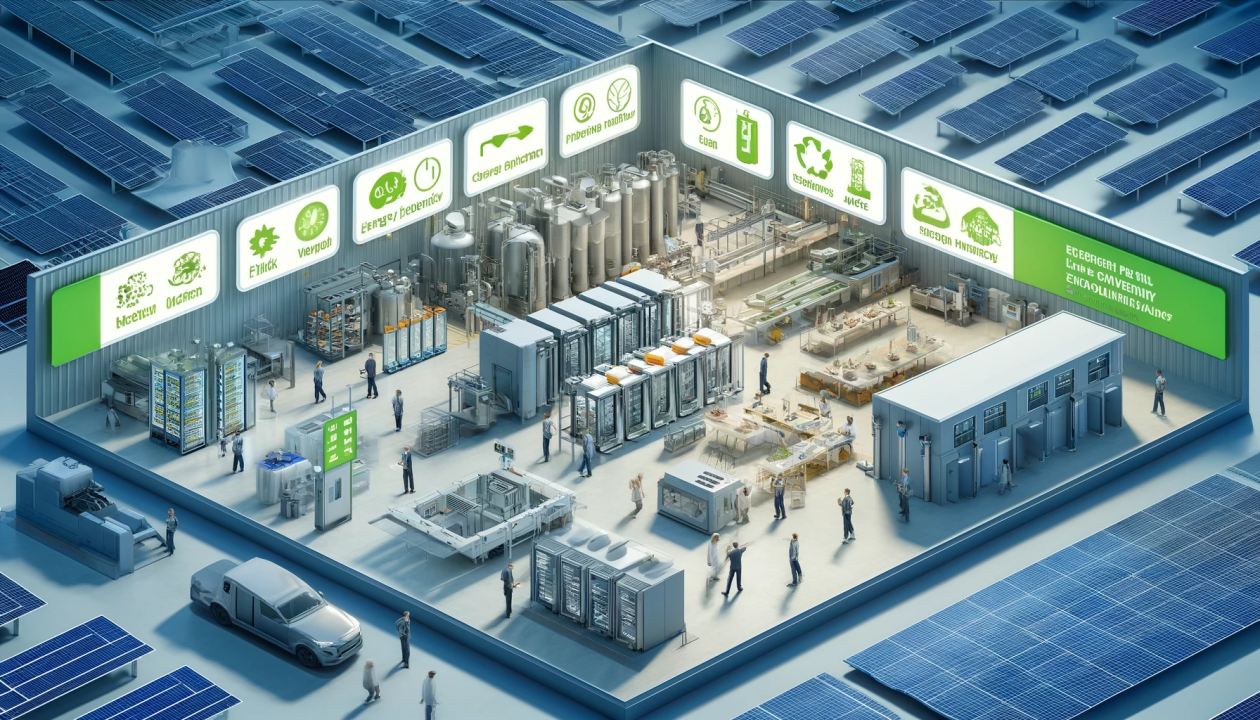
- Automation and Control Systems: Automated control systems can optimize energy use by adjusting equipment operation based on real-time data. For example, variable frequency drives (VFDs) can control motor speed and reduce energy consumption.
- Process Optimization Lean Manufacturing: Implementing lean manufacturing principles can streamline processes, reduce waste, and enhance efficiency. Techniques such as value stream mapping and continuous improvement can identify and eliminate energy wastage.
- Heat Recovery Systems: Installing heat recovery systems can capture and reuse waste heat from processes like baking, frying, and pasteurization. This recovered heat can be used for preheating water, air, or other processes, reducing overall energy consumption.
- Improved Insulation and Building Design Insulate Equipment and Facilities: Proper insulation of ovens, boilers, and refrigeration units can minimize heat loss and improve energy efficiency. Insulating buildings can also reduce the need for heating and cooling.
- Energy-Efficient Building Design: When constructing new facilities or renovating existing ones, incorporate energy-efficient design principles. This can include using natural lighting, optimizing HVAC systems, and implementing renewable energy solutions.
- Water and Waste Management Efficient Water Use: Implementing water-saving technologies and practices can reduce energy consumption associated with water heating and pumping. Reusing water where possible and fixing leaks promptly are also important.
- Waste-to-Energy Systems: Utilizing waste-to-energy systems, such as anaerobic digesters, can convert organic waste into biogas, providing a renewable energy source for the facility.
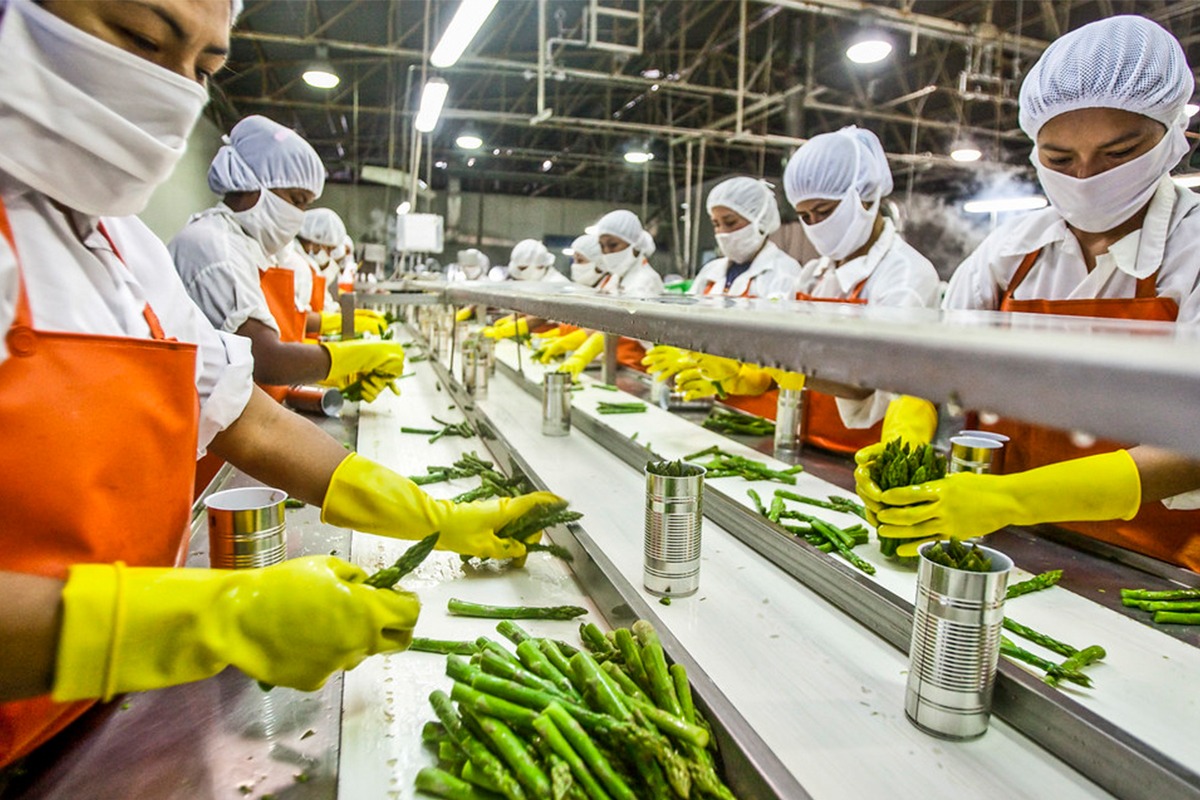
- Employee Training and Engagement Energy Efficiency Training: Educating employees about energy-efficient practices and the importance of energy conservation can foster a culture of sustainability. Provide training on how to operate equipment efficiently and identify areas of energy waste.
- Engagement Programs: Implement programs that encourage employees to suggest and participate in energy-saving initiatives. Recognizing and rewarding contributions can motivate staff to prioritize energy efficiency.
Case Studies in Energy Efficiency
- Dairy Processing Plant: A dairy processing facility conducted an energy audit and installed VFDs on its refrigeration compressors, reducing energy consumption by 15%. Additionally, the plant implemented a heat recovery system to capture waste heat from pasteurization, cutting its heating costs by 20%.
- Beverage Manufacturer: A beverage company upgraded its bottling lines with energy-efficient machinery and automated control systems, resulting in a 25% reduction in energy use. The facility also installed solar panels on the roof, generating renewable energy and lowering electricity bills.
- Bakery: A commercial bakery invested in high-efficiency ovens and improved insulation throughout its facility. By also adopting lean manufacturing practices, the bakery reduced energy consumption by 30% and decreased production costs significantly.
According to Linkin