Measure your current energy use
First, understand where your business is using the most energy, so you can find ways to reduce and save.
Based on the business’ we’ve worked with in the food and beverage manufacturing industry, the most common areas that use the most energy are:
Ways to reduce energy costs
1. Install a gas or electricity meter on high-energy equipment
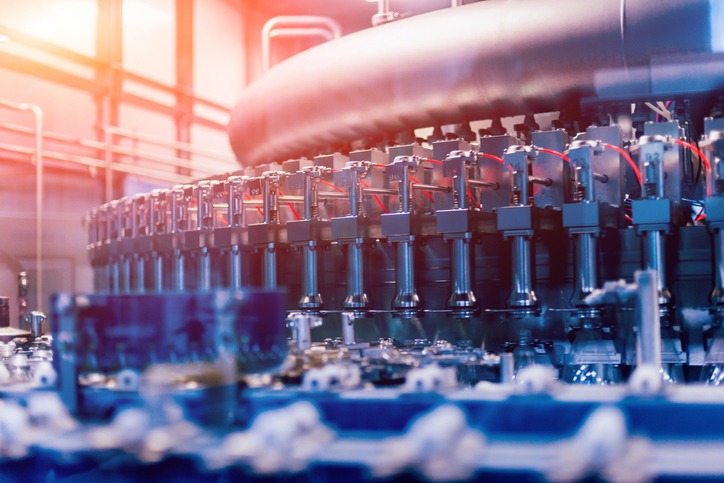
Buy and set up a gas or electricity meter on equipment that uses the most energy to monitor use.
The meter can show you how much energy the equipment uses and when. This data can be analysed to see if it’s working efficiently. You may find you can downsize equipment or discover when it needs maintenance.
Benefits
On average, food and beverage manufacturing businesses installing meters on high-energy equipment found they:
2. Implement heat recovery
Heat recovery is a process where you redirect and use heat that would otherwise be vented outside.
You can use the recovered heat to preheat water for boilers or heat the workplace.
Benefits
On average, food and beverage manufacturing businesses investing in heat recovery found they:
3. Add timers and operational controls to high-energy equipment
Some of your equipment may be running when it doesn’t need to be.
Add timers and operational controls to equipment that can be switched off overnight or when it’s not being used. This can take the effort out of training staff to manually switch equipment off.
Use timers to switch off equipment like:
Benefits
On average, food and beverage manufacturing businesses adding timers and operational controls to high-energy equipment found they:
4. Insulate piping
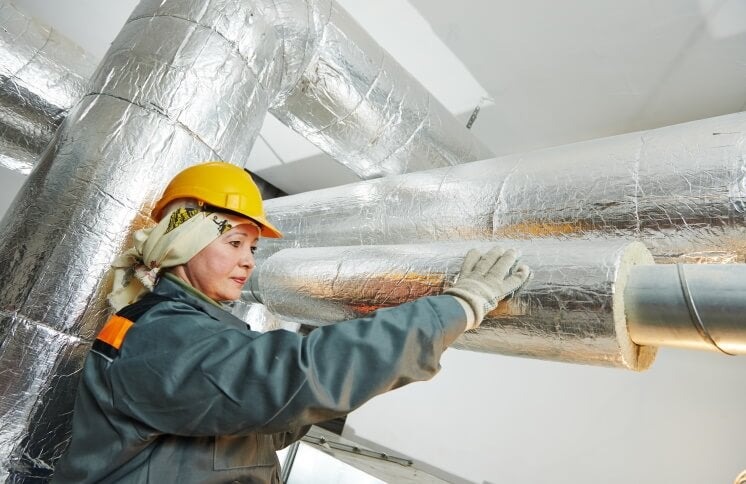
Insulating steam or chilled water piping will reduce heat losses and improve productivity.
Benefits
On average, food and beverage manufacturing businesses insulating piping found they:
5. Install variable speed drives
A variable speed drive controls the speed and frequency of a motor to match demand. If your process demand varies, you’ll reduce energy use and cost by installing a variable speed drive to:
Benefits
On average, food and beverage manufacturing businesses installing variable speed drives found they:
6. Maintain compressed air systems
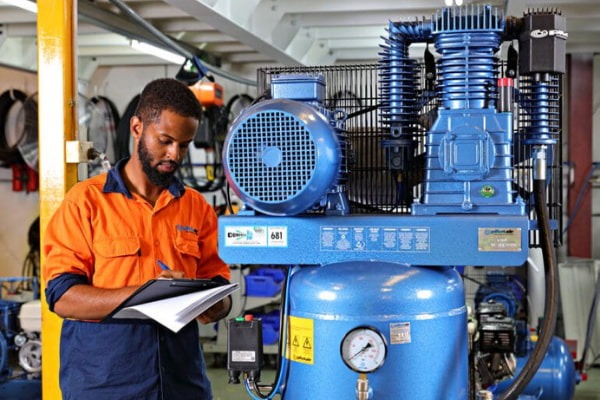
Apart from making sure you’re using the appropriate air pressure, you can also prevent wasting energy by regularly maintaining your compressed air systems, looking for:
Benefits
On average, food and beverage manufacturing businesses maintaining compressed air systems found they:
7. Invest in renewable energy
You can switch to renewable energy by:
Benefits
On average, food and beverage manufacturing businesses that invest in renewable energy found they: