Energy Efficiency and Conservation Practices at Coal Industry
Thứ ba, 01/07/2025 - 10:22
Many coal enterprises under the Vietnam National Coal and Mineral Industries Group (TKV) have been actively implementing electricity-saving practices, helping reduce production costs and ensuring energy security.
As a heavy mining industry, coal production consumes a significant amount of electricity. On average, TKV produces 40–45 million tons of coal annually, consuming over 700 million kWh of electricity. In the context of rising electricity prices and increasingly limited energy sources, electricity costs make up a substantial portion of coal production expenses. Therefore, using electricity efficiently has become a strategic objective for companies in the coal sector.
Saving Electricity in Core Production Processes
For example, to extract 2.5 million tons of coal, Ha Tu Coal JSC consumes about 22 million kWh of electricity, equal to 31–36.5 billion VND in production cost annually. As such, Ha Tu Coal is classified as a key energy user within TKV.
To both save electricity and maintain operational efficiency, the company developed a comprehensive energy efficiency plan, especially for high-consumption equipment. For drilling machines, they replaced soft-start inverters for drill motors and upgraded old oil circuit breakers to vacuum circuit breakers with digital relays at the 6kV switchboards. As a result, electricity consumption per meter drilled has decreased to 0.3 kWh, nearly half of what it used to be.
Similarly, electric excavators (EKG), used in the Bac Bang Danh project site, consume more than 5.3 million kWh annually. To improve efficiency, the company has optimized site preparation—such as workbench leveling, blasting, and machine platforms—to ensure continuous operation without idle time.
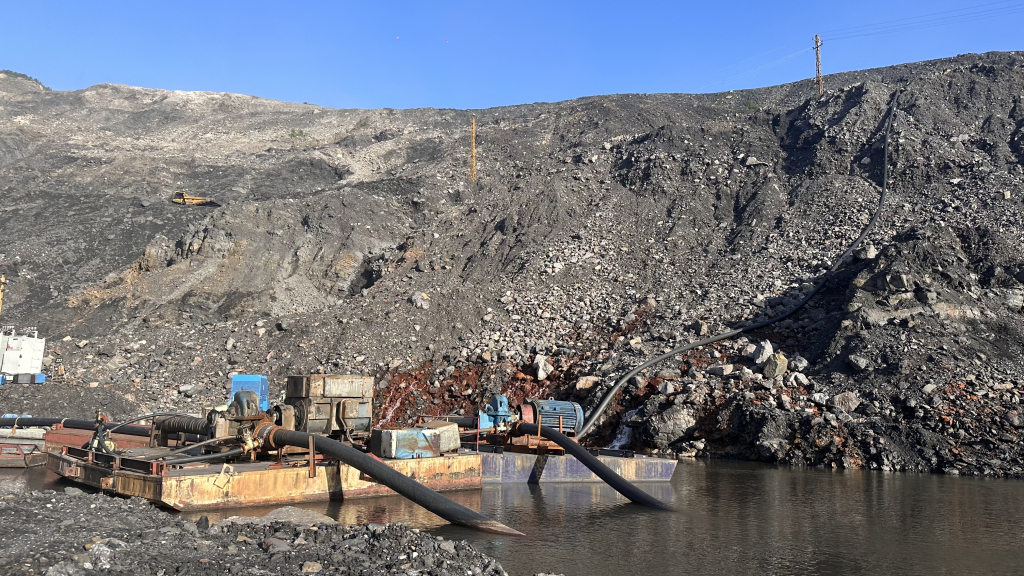
Intermediate pumping system at -40m level of Ha Tu Coal Joint Stock Company. (Photo: Quang Ninh Newspaper)
Ha Tu Coal has also optimized the mine dewatering pump system, which consumes a similar level of energy. They calculated water discharge strategies carefully to minimize forced drainage, a high-energy process. Pump stations were strategically placed to shorten electrical lines and pipe lengths, reducing voltage drops and energy losses.
Inverters and soft-start devices have also been installed on high-power pump motors. Additionally, dedicated transformer stations for the pumps are regularly inspected to prevent no-load operation.
Mr. Do Chi Dung, Deputy Head of Electromechanical Transport at Ha Tu Coal, noted: "The company has researched and proposed solutions to balance electrical loads and maintain a power factor above 0.9. This reduces reactive power consumption and helps optimize transformer load distribution. We aim to save 5–8% of total annual electricity consumption."
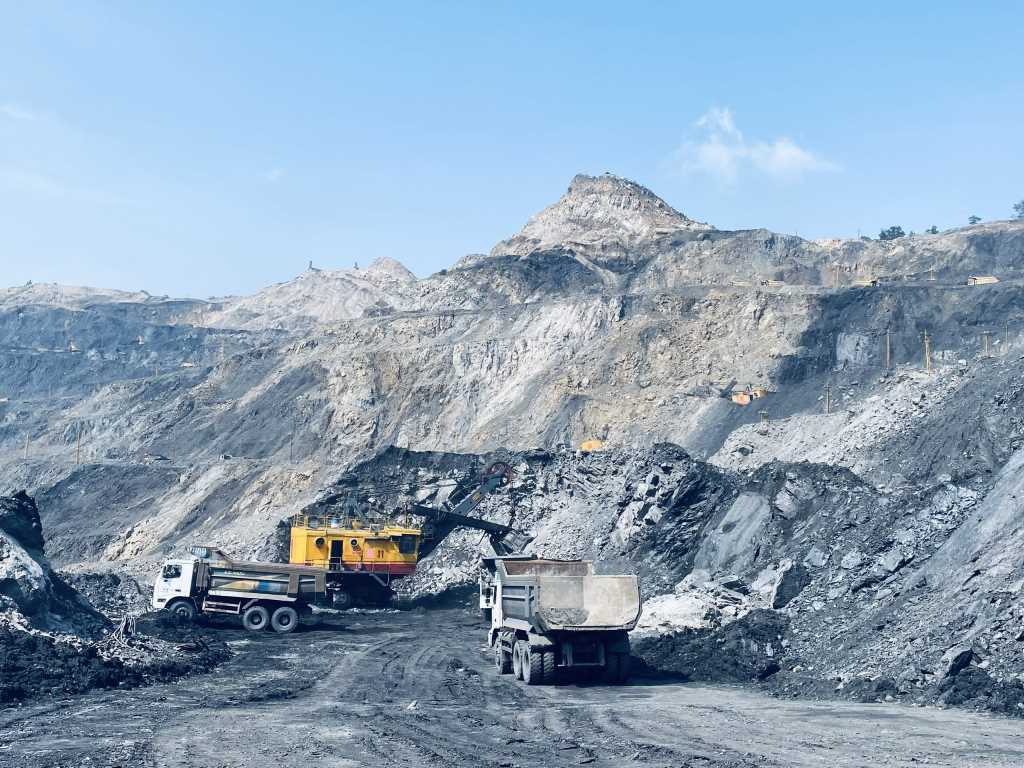
EKG electric excavator - one of the largest power-consuming devices at Ha Tu Coal Joint Stock Company. (Photo: Quang Ninh Newspaper)
In underground coal mines, mine ventilation accounts for 20–40% of total electricity use. Main ventilation fans are designed with motors ranging from hundreds to over 1,000 kW, operating 24/7 to ensure a constant air supply. Modern ventilation equipment in underground mines in the Quang Ninh region requires fans to operate at the maximum flow rate according to design calculations, which leads to high electricity costs for fan motors.
At the Dong Vong site of Uong Bi Coal Company, the main ventilation station (2x220 kW) supplies 145 million m³ of clean air for two working faces and seven development headings. It alone consumes over 237,000 kWh/month. Across the mine, nine additional fan stations of 18.5 kW or more are operating, contributing to substantial electricity usage.
Mr. Nguyen The Hung, Deputy Director of Uong Bi Coal Company, shared that to save energy, the mine adjusts the operating mode of fan stations based on real-time demand, rather than running fans at full capacity per design specs. They also use inverters to vary fan speeds, optimizing airflow and reducing ventilation energy costs, thus lowering coal mining production costs overall.
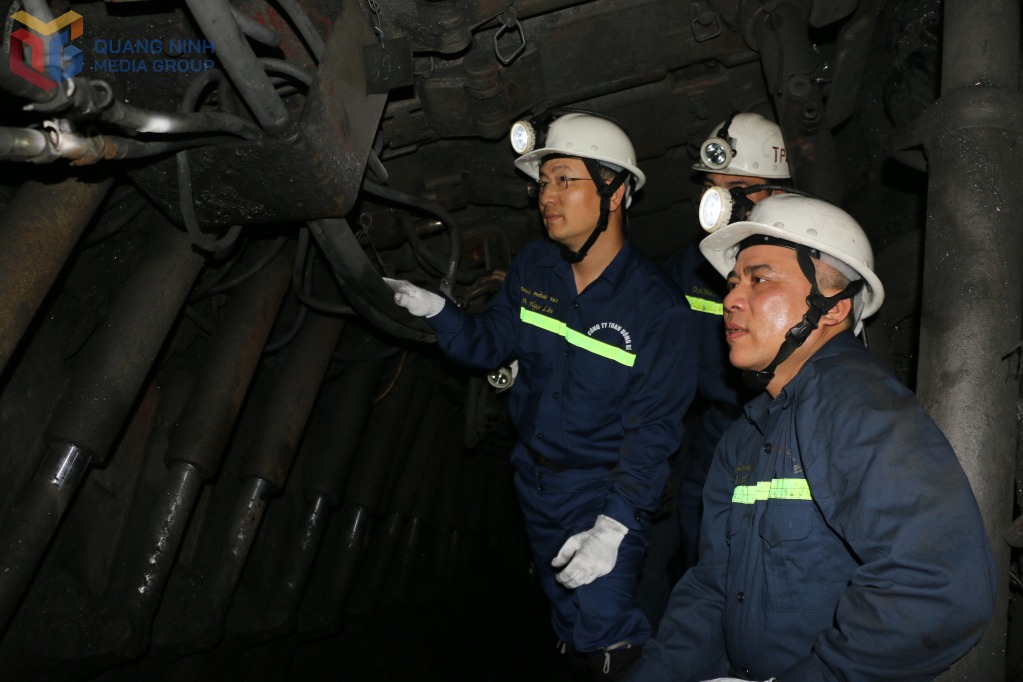
Leaders of Uong Bi Coal Company inspect the production situation in the market furnace. (Photo: Uong Bi City Website)
Efficient Energy Management
At many TKV subsidiaries, energy management is not just the technical department's job, but a routine part of executive operations. KPIs on energy saving, equipment efficiency, and power usage are closely tracked and integrated into performance evaluations, fostering innovation and proactive efforts across departments.
Several enterprises have invested in smart energy monitoring systems (EMS), enabling real-time tracking of energy usage by key equipment—ventilation fans, water pumps, drills, and excavators. The EMS alerts staff when consumption exceeds thresholds or equipment runs inefficiently. This reduces reliance on manual oversight and standardizes operations toward more transparent and professional management.
Beyond technical and managerial solutions, an energy-saving culture is emerging among workers. Many innovations come directly from frontline employees—such as modifying equipment operations based on load, improving motor cooling, or installing automatic shutoff sensors—saving tens of thousands of kWh each month.
Toward Sustainable Development
TKV has set a goal to reduce total energy consumption by 5–7% by 2025, cut electricity losses below 6.5%, and ensure 100% of key enterprises implement energy management systems. From 2026 to 2030, the target is to increase energy savings to 8–10%, moving toward “green mines” that operate efficiently and are environmentally friendly.
In summary, electricity-saving practices not only generate economic benefits but also enhance competitiveness and ensure sustainable development for coal enterprises, especially as energy prices rise and environmental regulations tighten.
The coordinated efforts from TKV's leadership down to individual business units—spanning technology and human resources—are driving a profound shift in mindset and practice across the sector. Every kWh saved is not just financial value—it represents TKV’s commitment to resource conservation, environmental protection, and green national growth.
DUC DO