One significant challenge is the garment manufacturing process itself. It is inherently complex and energy-intensive. And, as many factory managers also hesitate to invest in modern equipment due to high substantial financial costs, outdated machinery, and technology are often significant contributors to high energy consumption.
1. Conducting an Energy Audit: The first step towards reducing the consumption of energy is to conduct a comprehensive energy audit in your garment factory. An audit can give you a thorough look into energy usage patterns, garment machinery efficiency, and overall building efficiency. Based on this data, you can identify the areas that use the most and least energy, and which areas are rather inefficient and need improvement. In the longer term, manufacturers can consider using a data-based energy management system to monitor energy usage across the facility and make changes accordingly.
2. Investing in Energy-Efficient Equipment: This solution is pretty obvious. Manufacturing plants can first update their facilities by investing in LED lighting, and improving the insulation of the building, and should also consider updating their HVAC system if it is older than ten years. But, the investment does not stop there. Older garment machinery needs to be replaced as well, as newer technologies have more energy-efficient features. Especially machinery that is driven by a motor. According to ABB's 2022 Energy Efficiency Survey Report, upgrading industrial motor-driven systems could lead to a 10% reduction in global electricity consumption. Such machinery in a garment factory includes fabric spreading machines, fabric cutting machines, and fabric inspection machines.
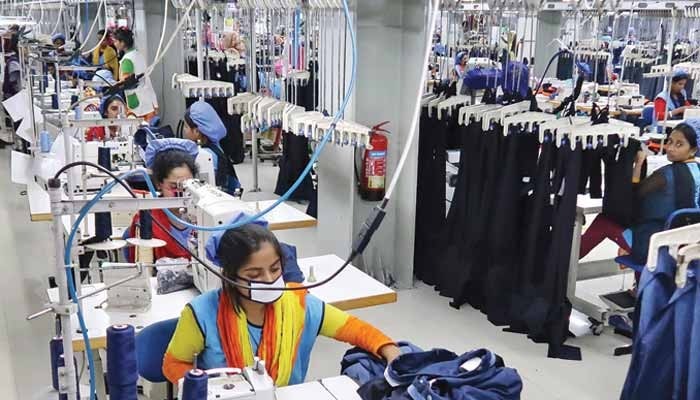
3.
Implementing Smart Manufacturing: We have often times emphasized the importance of new technologies in garment manufacturing before. And, one of their many benefits is their ability to optimize energy consumption by leveraging automation and data analytics. Adopting Industry 4.0 technologies like Industrial Internet of Things (IIoT), Artificial Intelligence (AI), or digital dashboards factories can benefit from a downtime reduction of 30-50% according to a 2022 McKinsey study
. For instance, a manufacturing company implemented IIot-enabled sensors in their packaging lines which has resulted in a 15% reduction of energy usage.
4. Cleaning and Maintaining Equipment: An investment into new energy-efficient garment machinery only pays off when they are well maintained. Regular cleaning and maintaining your equipment ensures their constant efficient operation, optimized performance, and long lifespan, which can translate to energy efficiency savings. Preventative Maintenance can also prevent energy waste due to malfunction or parts of machinery consuming more energy to work properly.
5. Optimizing Production Processes: Streamlining production processes minimizes energy consumption and improves productivity. Identifying and eliminating bottlenecks, reorganizing workstations, and implementing automation can enhance efficiency. The fastest and easiest way to optimize production processes is to implement a digital dashboard that gives garment factory managers a clear and thorough overview of all production data. With the help of this data, best strategies can be developed and executed.
6. Integrating Renewable Energy: Using renewable energy sources, such as solar panels, wind turbines, and geothermal systems, can reduce reliance on grid electricity for a garment factory. Although the initial investment may be on the higher side, the long-term savings and environmental benefits could justify the cost. Renewable energy infrastructure also enhances energy security and can generate additional revenue by selling excess energy back to the grid.
7. Training Workers and Staff: The proper training of garment factory workers should not be underestimated. As they are the pulse of the manufacturing process, training them on energy conversation is crucial. Strategies, such as thorough training programs or integrating the topic into onboarding processes can greatly impact saving energy in the factory facilities.
According to Linkedin